Lunety pod lupą
4. Niechciane odbicia
W latach 20-tych zeszłego wieku dwie firmy: niemiecka Carl Zeiss Jena i amerykańska Alvin Clark & Sons znalazły częściowe rozwiązanie problemu. Pomysł polegał na wypełnieniu szczelin między soczewkami obiektywu olejem. Olej, jako materiał znacznie gęstszy od powietrza, ma współczynnik załamania światła bliższy szkłu, przez co straty światła na granicy olej-szkło były dwukrotnie mniejsze niż na granicy powietrze-szkło. Pomysł ten za jednym razem zwiększał sprawność optyczną instrumentu i niwelował wewnętrzne odblaski. Jedyną wadą takiego rozwiązania było mętnienie oleju z czasem, co powodowało konieczność jego wymiany po kilku latach użytkowania.
Technologie rozwinięte w trakcie II Wojny Światowej znacznie posunęły do
przodu rozwiązania stosowane w refraktorach. Przed wszystkim zaczęto
intensywnie wykorzystywać powłoki antyodbiciowe. Na każdej granicy
ośrodków następuje bowiem zarówno załamanie jak i odbicie wiązki
padającego światła. O ile w przypadku obiektywu załamanie jest
zjawiskiem jak najbardziej pożądanym, bo dzięki niemu działa nasz
instrument optyczny, to odbicie jest tym czego chcielibyśmy uniknąć.
Światło obijające się od granicy ośrodków nie trafia bowiem do naszego
oka powodując spadek efektywności sprzętu. Strata niespełna 5% na każdej
granicy powietrze-szkło nie wydaje się na pierwszy rzut oka duża, ale
jeśli uwzględnimy, że straty następują zarówno w obiektywie jak i w
okularze, to liczba granic ośrodków potrafi sięgać dziesięciu, a straty
światła na tych granicach ponad 40%.
Aby zaradzić temu problemowi producenci refraktorów pokrywają elementy optyczne tzw. warstwami antyodbiciowymi znacznie podwyższającymi transmisję światła na granicy ośrodków. W rzeczywistości warstwa antyodbiciowa to nic innego jak cieniutka powłoka materiału takiego jak fluorek magnezu (MgF2), dwutlenek krzemu (SiO2) czy dwutlenek tytanu (TiO2).
Zasada działania warstw antyodbiciowych opiera się na zjawisku interferencji fal elektromagnetycznych. Chodzi tu o to, aby tak dobrać grubość warstwy i jej współczynnik załamania aby fale odbite od granicy powietrze-warstwa i od granicy warstwa-szkło wygaszały się wzajemnie tzn. były przesunięte w fazie o 180 stopni. Aby uzyskać ten efekt za pomocą jednej warstwy jej grubość optyczna musi być nieparzystą wielokrotnością 1/4 długości fali padającego światła.
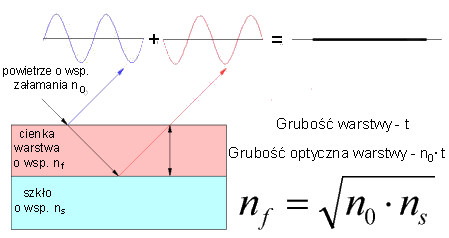
W praktyce, w przypadku jednej warstwy, najczęściej stosuje się fluorek magnezu (MgF2), który działa skutecznie dla długości fal od 400 do 750 nm i dla szkieł o współczynniku załamania od 1.45 do 2.4. Poniższy rysunek pokazuje zależność odbijanego światła od długości fali dla szkła typu Bk7 bez żadnej warstwy i z pojedynczą warstwą MgF2. Pokazano krzywe dla wiązki światła padającej prostopadle (0 stopni) i pod kątem 45 stopni. Widać wyraźnie, że od szkła niepokrytego odbija się średnio 4.25%, a od szkła z nałożoną warstwą tylko 1.5%. Jak widać na rysunku, jedna warstwa najskuteczniej działa dla środka zakresu widzialnego czyli długości fali 550 nm, na którą nasz wzrok jest najczulszy. Aby dodatkowo zmniejszyć ilość odbijanego światła zarówno w długości fali 550 nm, a także w całym zakresie widzialnym stosuje się warstwy wielokrotne (ang. multicoating), gdzie na szkło nakłada się kilka warstw o różnej grubości, tak aby efektywnie wygaszały się odbijane fale o różnych długościach. Współczesne warstwy renomowanych producentów są tak zaawansowane technologicznie, że od jednej granicy powietrze-szkło odbija się tylko 0.1-0.2% światła.
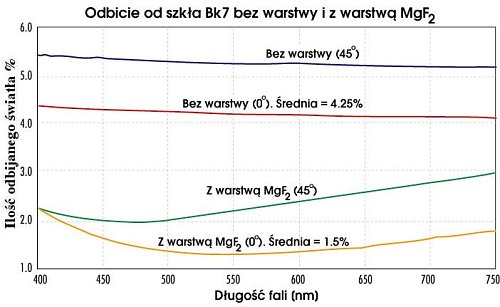